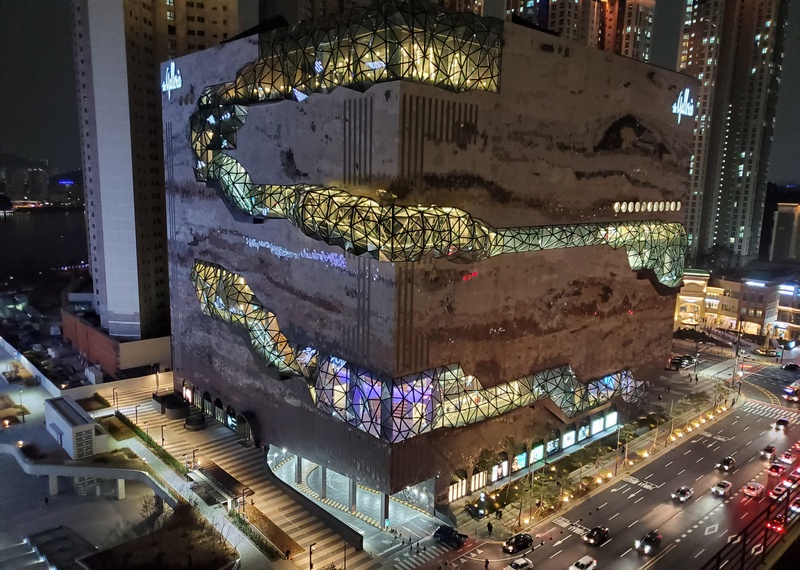
From its rustic yet modern facade to the intricately engineered elevation, Galleria in Gwanggyo is a landmark building located in the new town of Gwanggyo, South Korea. The Galleria is notably Korea’s first and largest upscale department store franchise, founded in the 1970s, and has remained at the forefront of the luxury retail market since. The new store in Gwanggyo is located at the center of young urban development, surrounded by tall residential buildings. The store’s stone-like appearance makes it a natural point of attraction for the public residing in the town of Gwanggyo.
(按此瀏覽中文版)
The building is located between the Suwon Gwanggyo Lake Park and the tall buildings in the city. It marks an intersection between nature and the urban landscape. At first sight, the building presents a strong heaviness and massiveness that form the building’s architectural language. Lateral interventions on facade cut the building with pixelated glass volumes – serving as a public route, which are protruded from the building, to soften the heaviness of the building. The storefront features a textured mosaic stone facade that elevates the nature of the neighboring park—appearing as a sculpted stone coming from the ground, making it a visual anchor to the town of Gwanggyo.
The exterior of the building is designed as an irregular shape of curtain wall, and this was only possible because of the WITHOWRKS team’s extensive research and intricate detail of physics and modern structural engineering. The team thoroughly understood the challenges that the existing methods could not address the requirement. The curtain wall is made with three different flat glass shapes connected via different deflection angles. This requirement caused challenges, such as the vertex deflection phenomenon. However, with the help of the Smart Node system developed especially for the Galleria department store (GDS), the team was able to address the challenges. In addition, additive manufacturing (AM) technology was used in production, showing an intricate method for irregular façade construction.
One of the key achievements is that the developed Smart Note system performed with 99.4% construction accuracy, where only 10 out of 1652 glass sheets required reworks or corrections.
3D Printing-applied construction: Smart node system for an irregular building façade
In the GDS project, 30–50 Smart Nodes were cast according to the size for each charge, and one material report was issued for each charge. 15 charges were cast, and 15 tensile test results are shown in the figure below. The yield strength was 439.6 MPa on average, performing at 123.8% compared to the standard value (355 MPa).
The development of the Smart Node & Glazing Design used in the project
To address the challenges, a hollow free-form shell node must be displayed together with glass. The below image shows the schematic design of the hollow node, named Smart Node. Smart Node provides a merged point and simplifies the glazing system. As a result, the required vertical span between the structural member and glazing part had to be shortened from 150 to 220 to 100–130 mm, to help mitigate the vertex deflection phenomenon.
Smart Node Manufacturing: 3D Printing Method
The main challenge in producing the smart nodes is finding the production method for the 647 nodes while meeting the time and cost requirements. Testing 3D sand printing confirmed several benefits. First, 3D printing laminates the sand directly with the binder without making a wax pattern, reducing the time required to make a sand mold. Then a thermal simulation was added through the thermal analysis program, which could shorten the existing test production process from two weeks to several days. Besides the shaping accuracy of the 3DP method, the integrated thermal simulation method was available to reduce the required time for each cycle. In addition, the smart node production system simulated the mold of the next charge while 3D printing.
This made it possible for each cycle to be carried out continuously in parallel. Due to the hollow construction, the mold comprises three parts: the lower mold, core mold, and upper mold, the production process of Smart Node from the design and simulation to completion. The lower mold supports the whole mold, the core mold hollows the inside of the smart node, while the upper mold carries out casting methods, such as gate and riser. The three parts were analyzed in advance through simulation software, such as Magma, and the mold was designed in a shape that can minimize temperature shrinkage deformation and air bubbles. After the simulation, the parts were 3D printed by a binder jetting machine. Each smart node was produced as required by the project plan, and the three parts were assembled to make a mold and cast the steel alloy. 4.2. System inspection and performance tests.
Smart Node with a hollow interior is manufactured using 3DP and weighs about 15 kg. The Smart Node system is advanced compared to the existing node systems considering production period, weight, construction error, number of arms of the node, glass angle condition, and the aesthetic function as an interior material, as verified in this paper. In addition, the Smart Node system has advantages in manufacturing irregular shapes, achieved by AM technology. One of the significant lessons from this project is how to secure the cost-effectiveness of novel technology adoption. In the GDS project, the team tried to minimize the required number of nodes by design optimization, by which the project could achieve practically effective implementation. Compared to traditional methods, new methods have limitations, such as limited resources and a lack of practitioners’ understanding. Only three sand binder-jet 3D printers were used during project manufacturing to produce the nodes.
All in all the OMA along with WITHWORKS have created a structure that is going to steal the attention of the town. The multifaceted glass facade covering the building is also a public route. Through the glass, retail and cultural activities can be witnessed by the city’s passers-by, while visitors on the interior can enjoy new vantage points to experience the beauty of Gwangyyo. In addition the public loop also offers spaces for exhibitions and performances.