PRC Magazine speaks to TK Elevator about the benefits of MiC and its new milift® modular elevator solution.
(按此瀏覽中文版)
German mobility solutions and engineering expert TK Elevator has announced the first commercialised modular elevator solution in Hong Kong. Known as milift®, it combines the company’s Machine Room-less (MRL) elevator solutions with Design for Manufacturing and Assembly (DfMA) and Modular Integrated Construction (MiC) concepts to offer unprecedented advantages over conventional elevator installation methods, designed specifically for installation and retrofits to overhead bridges, low-rise buildings and various other applications.
TK Elevator’s Hong Kong office was established in the city over 20 years ago, and has over time developed long-standing partnerships with the city’s construction and public works sector, working with its customers to deliver innovative and market-leading mobility solutions. The company’s latest offering, milift®, was introduced in support of the government’s promotion of the MiC building concept. TK Elevator is the first company to develop a modular elevator solution in Hong Kong, in the form of an overhead bridge in Tuen Mun in the Western New Territories.
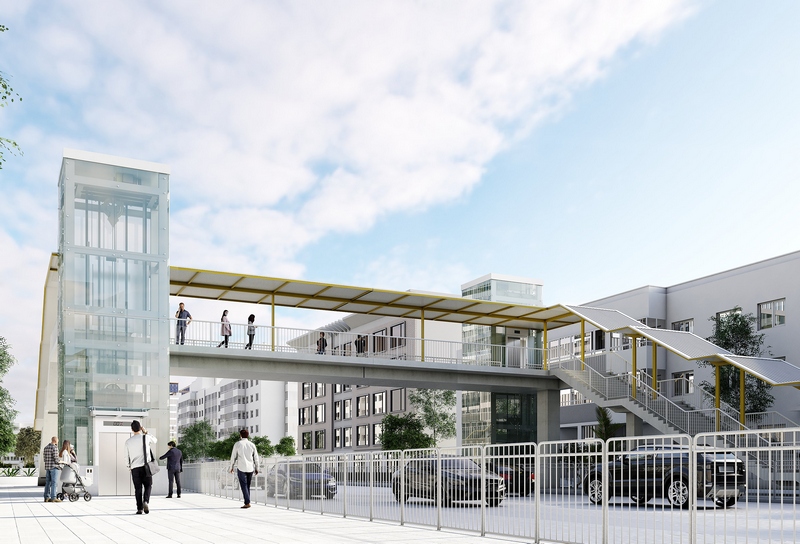
Taking full advantage of the Greater Bay Area Initiative, manufacturing and assembly of the milift® take place in a Mainland facility in the Guangdong province, before it is transported and installed on site in Hong Kong.
First introduced in the 1970s, DfMA and MiC technologies have been applied in escalators and moving walkways for quite some time. However, the technology has not been popular in elevator systems until now. According to Dr. Andy Chan, industry veteran and now a consultant for TK Elevator, DfMA is the guiding principle and MiC is the concept. Similar applications are found in building structures, electrical and gas installations, fire service and piping works. In terms of elevator systems the benefits include reduced construction time and on-site labour, improved product quality and safety due to precise factory prefabrication in a controlled environment, and the avoidance of time loss and work stoppage arising from incumbent weather conditions. The standalone yet integrated modules are delivered for on-site assembly, replacing the traditional on-site installation and assembly of components and parts.
Within the elevator industry, few have been able to master the potential of the MiC concept, largely due to the coordination required between contractors and end customers, and constraints relating to regulatory requirements, logistic complexity and suitable venues for prefabrication works. However, despite the challenges, TK Elevator has been the first to market and milift® presents a viable solution
suitable for overhead bridges and other low-rise buildings, using a technology that in time may well be extended to cater for a wider range of applications.
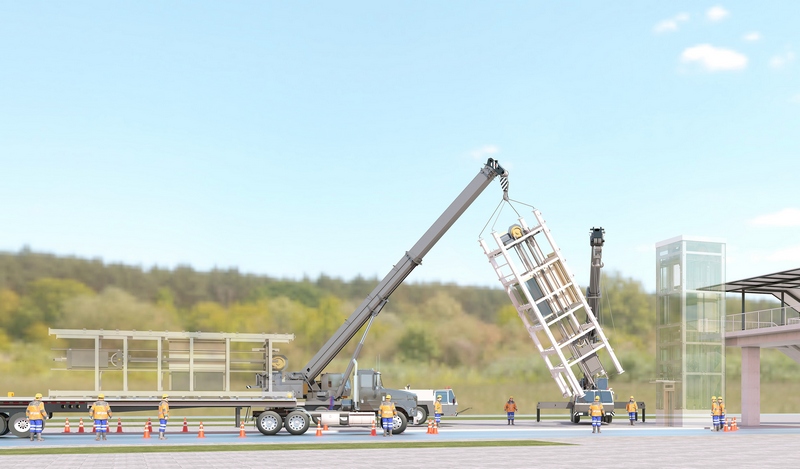
BACKGROUND
The Hong Kong SAR Government has been actively looking at ways to shorten the construction cycle time and proactively drive MiC application in the construction industry. In fact, the adoption of MiC in the public sector, including BD, ArchSD, HKHA, community and institutional buildings, as well as in the private sectors was first highlighted in the Chief Executive’s 2018 Policy Address, and again in the 2021 address. The Construction Industry Council (CIC) and the Electrical and Mechanical Services Department (EMSD) took the initiatives to provide advice and guidance to various trades seeking MiC implementation.
Socially too, amidst an increasing demand for barrier-free facilities in the community including overhead bridges, public transport systems, as well as properties located in areas suitable for the use of horizontal and vertical transportation means and facilities, and a need to minimise disruption caused to the general public by building construction, MiC offers a realistic and viable solution, particularly in a post Covid-19 environment and shortage of labour relating to new installations.
As such, the benefits of the Greater Bay Area Initiative make MiC a practical solution and application in terms of accessibility of prefab venues, transportation and logistics management, custom clearance, and works integrations of different contractors.

DESIGN PRINCIPLES AND METHODOLOGY
The design principles and methodology consist of offsite prefabrication which encompasses multi-trade integration, module maximisation and the final on-site ‘plug and play’ phases.
“It’s a methodology that consists of an integrated design featuring offsite factory fabrication and assembly, logistics or transportation to site, through to onsite installation, testing and commissioning,” said KC Chan, Managing Director of TK Elevator Hong Kong. “With MiC applications a current and future trend in the construction industry, we are confident of milift®’s potential in the market as a first mover.”
The majority of milift® installation, consisting of the brackets and fixings, guide rail, car cage, counterweight, machine; controller; electrical works, including trunking, conduit, and wiring; and finally, temporary fixing for transportation takes place at the factory in Guangdong. Here, highlights of the work include plumb line setting where templates are connected horizontally according to GAD design to ensure they are level, and the guiderail brackets are positioned precisely onto the bracket fixed onto the shaft steel structure.
With most of the elevator equipment now installed inside the structural shaft, the milift® is then transported to the site in Hong Kong, where on-site installation consists of hoisting the milift® and the structural shaft to its vertical position and fixed onto the superstructure, all completed overnight. The roof and the façade is then added to the superstructure and handed back for completion of final testing and commissioning, ready for statutory inspection and the final issuance of the use permit, according to TK Elevator’s protocol and statutory requirements.
BENEFITS OF milift®
The benefits of milift® are multiple, not least that the time required for total lift installation, testing and commissioning at site until ready for statutory inspection is anticipated to be reduced by as much as 70% when compared to traditional site installation work. Damage to equipment, loss of materials and wastage at site is minimised and limited site work reduces works at site significantly, hence mitigating safety risks. With the overall time for site works having been reduced, site resources are also minimised, while an improved quality of works is achieved due to close to 90% of parts and components having been assembled in a well-equipped prefab plant environment.
“Although the overall cost of works may not be reduced significantly, the practical benefits such as shorted construction time, reduced site works and site resources, increased quality and safety and reduced wastage are crucial in construction works, and can make a valuable benefit to the community in terms of increased accessibility,” concludes Dr. Johnny Leung, TK Elevator’s CEO Southeast Asia.
For further details, please visit tkelevator.com.