Since 1962, mechanical and electrical consulting engineering giant J. Roger Preston Limited (JRP) has had a hand in the functioning of some of Hong Kong’s most recognisable landmarks, among them Ocean Terminal, the Hong Kong Coliseum, Exchange Square, Jardine House and Hongkong Bank Headquarters.
Today, 55 years on, the company employs over 600 staff in offices across Asia, in Hong Kong, Beijing, Shenzhen, Shanghai, Macau, Kuala Lumpur, Singapore and Ho Chi Minh. The company is also involved in notable engineering works spanning the region, including projects in Nanjing, Shenyang, Wuxi, Foshan, Xiamen, Guangzhou, Dalian, Kunming, Harbin, Chongqing, Hainan, Jakarta, Phnom Penh and Mumbai.
As the company embarks on its 56th year, it continues with the same sense of purpose it was founded on and the old adage still rings true:
JRP – Your trusted engineering partner.
By the 1980s, JRP had become market leader in Asia’s mechanical and electrical engineering industry, and the local Hong Kong office had claimed its independence from its UK parent.
“People were eager to work for JRP. We were the company everyone wanted to join to earn the reputation, the knowledge, and the experience for a career,” notes director, Victor Cheung.
Few could deny that the world of engineering has seen drastic changes since JRP first opened its doors in Hong Kong, not least the gradual shift towards Building Information Modelling (BIM). However, since its work on Kai Tak Airport, JRP’s first project in the city, Cheung acknowledges that some things remain strikingly similar: “The fundamental engineering principles of air conditioning, for example, haven’t changed much in the past few decades. We’re still moving air through sheet metal ducts and distributing it through air grilles. But today the way we do it is more efficient. Equipment are getting more compact and energy efficient, and control system are becoming more sophisticated and intelligent. Variable speed drives are widely used for fan, pumps and chillers nowadays,” he adds. “Technology and innovation are driving these changes. We use tools such as Computational Fluid Dynamics (CFD) analysis and BIM to optimise the design in terms of cost effectiveness and buildability. The other major breakthrough is the chilled beam air-conditioning system which we have successfully implemented in a few projects in Hong Kong in recent years.”
The Rise of the Supertall
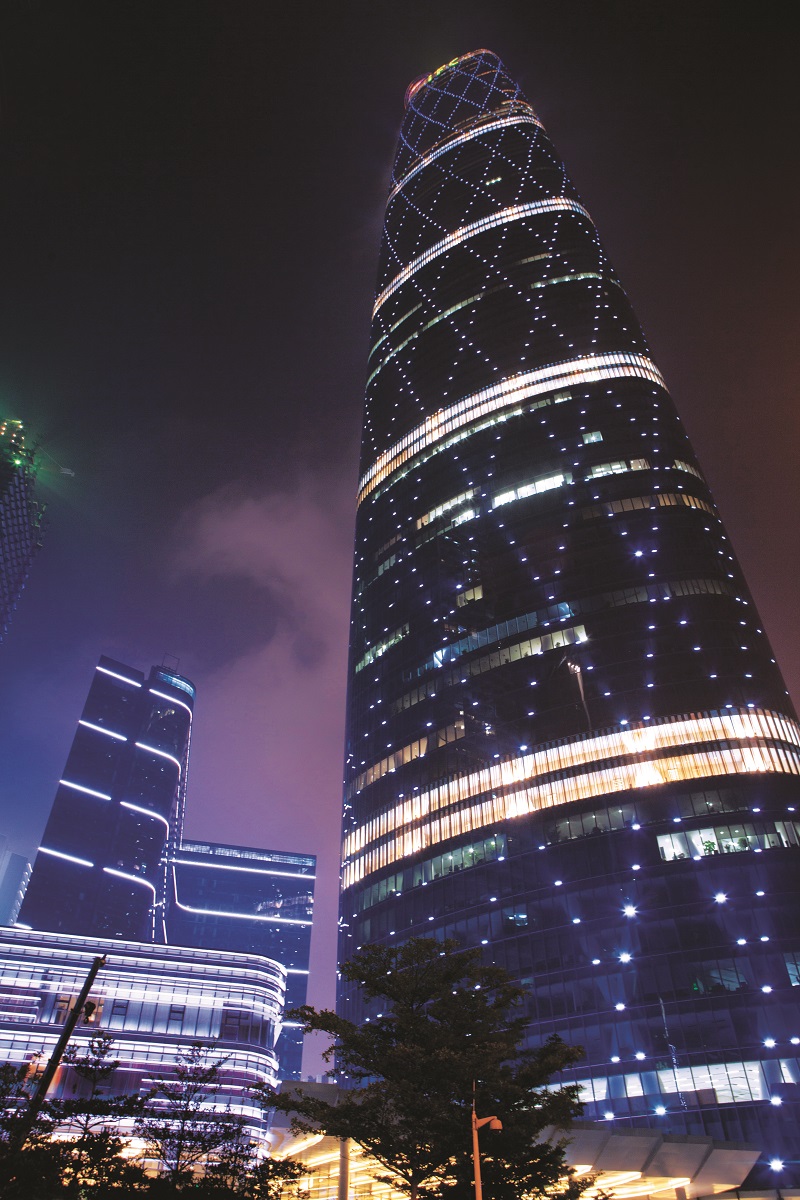
Guangzhou International Finance Centre, also known as Guangzhou West Tower
JRP has become the regional industry leader for mechanical and electrical engineering for its ability to bring solutions to commercial, hospitality, heritage, education, healthcare, retail, residential, cultural, recreation, infrastructure, institutional and industrial facilities. But if JRP has to claim a speciality it is perhaps in the supertall sector. That started in 1985 with the construction innovation of its time, Hongkong Bank Headquarters, designed by Norman Foster and just shy of 180 metres. “It was significant because of its location. It was in Central, and you couldn’t have lorries blocking Queen’s Road. It was the first instance of non-in situ construction. It was modular and pre-fabricated off site,” explains JRP director Joseph Leung.
“Air-conditioning plant, toilets, air ducts and pipes modules were all pre-assembled in Japan and brought in to Hong Kong. The parts were then trucked in from the harbour at night and stacked up like legos. Another innovative design for the project was that the air conditioning was supplied from underfloor.”
After that came tower after tower, including the city’s first supertall, the 420 metre high Two International Finance Centre (Two IFC). The 108-storey International Commerce Centre (ICC) followed, checking in at 490 metres, then the 432 metre Guangzhou IFC and the 468 metre Tianjin R&F Guangdong Tower.
The latest addition to JRP’s supertall portfolio is the Kohn Pedersen Fox-designed Ping An Finance Center in Shenzhen. At 599 metres and115 storeys high, it is the tallest building in Shenzhen, the second tallest in China and the fourth tallest building in the world. “Designing a reliable, efficient and sustainable building services system for this world class, supertall building posed formidable challenges to all engineers. JRP deployed the same team of experienced engineers who worked on the ICC building in Hong Kong. In collaboration with the project team, reliable, efficient and sustainable engineering solutions have been brought about,” notes director, HK Yung.
Like most supertalls, Ping An presented a host of engineering challenges. “The first thing any architect must think about is efficiency. Clients need to be able to benefit from a very efficient floor plate and get a good rental return from the height,” explains Leung. Yung adds: “Our job is to design an effective core that accommodates lifts, lobbies, toilets, mechanical, electrical, fire services, plumbing and drainage.”
Maximising gross floor area is key for investors looking for blue chip tenants, and central cores are an industry mainstay for that reason, offering tenants and landlords better views and better façades. Understanding usage also plays a part, particularly when finance occupiers and five-star hotels increasingly share supertall towers. Financial tenants and hotel guests have little interest in spending an inordinate amount for time waiting for lifts, making peak hour capacity one of the most complex systems for any mechanical and electrical engineer.
“Those same finance tenants may keep irregular hours due to trading times, but everyone gets hungry at about the same time and how do you handle that?” asks Leung. “With supertalls, hotel tenants present a specific set of requirements and demand a sense of exclusivity,” he adds. Yung further explains: “It’s a totally different approach. Basically, a high-rise building is a number of smaller buildings stacked together. Every single high-rise building shares the same challenges, and one must consider how you get people to each floor efficiently, how you distribute the power supply efficiently, how you ensure you’re not putting too much pressure on the hydraulics, whether the air conditioning system is seawater cooled and whether there is room on the roof or on the mechanical floor for cooling towers. You need to break the building down into several zones, and think of every zone as one building,”
Healthcare Excellence
Also among JRP’s core competencies is health care. Indeed, the company is responsible for a vast number of Hong Kong’s hospital engineering. Health care facilities are defined by a radically distinct set of mechanical and electrical needs from their supertall counterparts. “There are different demands for air conditioning and infection control in a hospital environment,” states Cheung. “You need to pump in good air, extract the old and never let them mix. Cross contamination can’t happen; there’s a pressure regime that needs to be maintained, and particulates need to be filtered out first. You also have to consider other mechanical services such as medical gases, pneumatic tube systems, IT systems, a high demand for hot water and power supply, back up generators and a high air conditioning load, as well as reliability and energy efficiency.”
JRP’s credits in the sector include the Queen Mary Hospital expansion, Canossa Hospital extension, Ruttonjee Hospital, Yan Chai Hospital, United Christian Hospital, Union Hospital extension, Nethersole Hospital, North Lantau Hospital and the forthcoming Hong Kong Children’s Hospital (HKCH) at Kai Tak, which will host 468 beds and 13 operating theatres in a two-tower, podium-free building connected by three bridges.
HKCH is a point of pride for JRP, with space designed for research, training, integrated rehabilitation, clinical services, surgical theatres and the hospital’s data centre. It is also the first facility of its kind in Hong Kong purpose-built with 900 square metres of solar and hot water panels on the roof – the largest renewable energy installation in the waterfront of Victoria Harbour. “Hospitals are the ideal application of solar hot water systems,” says Cheung. The design and engineering won the hospital the highest Platinum BEAM Plus rating from the Hong Kong Green Building Council (HKGBC) for environmental sustainability. HKCH is the first hospital project to achieve such high standard, making it the Greenest hospital in Hong Kong. Chilled water for air-conditioning the hospital comes from the Kai Tak District Cooling System – a project successfully completed by JRP two years ago.
Government projects are mandated to build to BEAM Gold standards, and with JRP, HKCH exceeded that minimum. Yung defends the perception that Hong Kong isn’t doing enough on the sustainability front. “If you want a platinum rating you have to do a little bit more,” he adds.
The Future of Data
A pillar of Hong Hong’s business competitiveness and a burgeoning property sub-sector set to grow in the coming few years is data centres. As the world becomes more and more digital and Big Data and the Internet of Things (IoT) becomes the norm, banks and financial institutions, schools, retailers, and social media will demand more and more storage and data processing power. Like supertall towers and hospitals, data centres have a unique set of hurdles to consider and overcome. “The government is keen to support this sector, and are releasing out land to attract tenants,” explains Leung. “They are the most energy-hungry projects going, even more than hospitals, with the data racks needing to be constantly chilled to ensure they perform 24 hours a day throughout the year.”
JRP has completed numerous data centres that are now storing data for Morgan Stanley, JP Morgan, American Express, Wochovia Bank, Citigroup, UBS and the Hong Kong Monetary Authority, Tamar Government Headquarters, as well as a series of Mega-iAdvantage Data Centres in Hong Kong, Singapore, Shanghai and Beijing. The HSBC secondary group data centre completed two years ago at Shatin can host up to 4,000 racks. The new China Unicom Global Centre in Tsueng Kwan O will host upwards of 4,000 racks. Unique as their demands may be, Leung argues there are three fundamentals that must be met in all data centre projects. “Data centres are highly specialised. In terms of design for a data centre there are three ‘Rs’ that must be adhered to which are also non-traditional,” he explains. “The first is Reliability, because if your Visa card doesn’t work on occasion, it’s their fault. The second is Resiliency, meaning one mission-critical system can back up another without jeopardising its overall operation. The last is Redundancy. You have to build with enough space and capacity for future growth.”
China Unicom’s Global Centre will host Internet data, cloud services and cross-border network services, with distinct centres focused on servicing the Asia-Pacific region in the Global Solution Support Centre, as well as an international Innovative Service System Centre and Cloud Computing Centre, and an IoT Research and Development Centre.
Hong Kong is uniquely positioned to host data facilities due to its combination of power supply reliability ﹣ a global best ﹣ and security in relation to the network. Leung points out the sector has been booming for nearly a decade, and that land has already been earmarked by government in Tai Po and Tseung Kwan O, complete with specially built infrastructure for power and other utility services support.
Healthcare Excellence
Also among JRP’s core competencies is health care. Indeed, the company is responsible for a vast number of Hong Kong’s hospital engineering. Health care facilities are defined by a radically distinct set of mechanical and electrical needs from their supertall counterparts.
“There are different demands for air conditioning and infection control in a hospital environment,” states Cheung. “You need to pump in good air, extract the old and never let them mix. Cross contamination can’t happen; there’s a pressure regime that needs to be maintained, and particulates need to be filtered out first. You also have to consider other mechanical services such as medical gases, pneumatic tube systems, IT systems, a high demand for hot water and power supply, back up generators and a high air conditioning load, as well as reliability and energy efficiency.”
JRP’s credits in the sector include the Queen Mary Hospital expansion, Canossa Hospital extension, Ruttonjee Hospital, Yan Chai Hospital, United Christian Hospital, Union Hospital extension, Nethersole Hospital, North Lantau Hospital and the forthcoming Hong Kong Children’s Hospital (HKCH) at Kai Tak, which will host 468 beds and 13 operating theatres in a two-tower, podium-free building connected by three bridges.
HKCH is a point of pride for JRP, with space designed for research, training, integrated rehabilitation, clinical services, surgical theatres and the hospital’s data centre. It is also the first facility of its kind in Hong Kong purpose-built with 900 square metres of solar and hot water panels on the roof ﹣ the largest renewable energy installation in the waterfront of Victoria Harbour. “Hospitals are the ideal application of solar hot water systems,” says Cheung.
The design and engineering won the hospital the highest Platinum BEAM Plus rating from the Hong Kong Green Building Council (HKGBC) for environmental sustainability. HKCH is the first hospital project to achieve such high standard, making it the Greenest hospital in Hong Kong. Chilled water for air-conditioning the hospital comes from the Kai Tak District Cooling System ﹣ a project successfully completed by JRP two years ago.
Government projects are mandated to build to BEAM Gold standards, and with JRP, HKCH exceeded that minimum. Yung defends the perception that Hong Kong isn’t doing enough on the sustainability front. “If you want a platinum rating you have to do a little bit more,” he adds.
The Hospitality Boom
With the hospitality sector in Asia witnessing the fastest growth in the world, the region is set to see biggest pipeline of new hotel stock in coming years. Hotel clients are as frequent at JRP as any other, and the number of engineering projects in the hospitality industry is unlikely to soften in the years ahead. A diverse portfolio that includes the Peninsula, Four Seasons, Ritz Carlton, Sheraton, Mandarin Oriental, MGM Grand and the City of Dreams in Macau, Hong Kong Polytechnic University’s Hotel ICON ﹣ comprising a hotel, a teaching hotel, and a senior staff quarters ﹣ Swire’s cutting edge design Hotel EAST, the W Guangzhou and the singular, tiered, Langham Hotel in Pazhou, has taught JRP that the key to efficient mechanical and electrical engineering for hotels comes down to meticulous design coordination for all guest contact areas suiting their brand identity.
“You need to know who your hotel operator is,” Leung reasons. “If it’s Four Seasons or St. Regis, you don’t opt for the very fancy stuff. You go for the classic knob to dim or turn off the lights. If your client is the W Hotels & Resorts, you go for sophisticated design and touch screen technology. The market positioning of the hotel defines the engineering, just as the client sector drives the services.”
It is a philosophy that comes into play with the new Ritz-Carlton Hotel in Harbin, part of a mixed-use development. One of three towers in the project, the Ritz-Carlton will stand 288 metres tall, and upon completion in 2019 will be Harbin’s tallest building.
PingAn Finance Center E&M Highlights
The Ping An Finance Centre achieved LEED Gold and 3-star rating for its environmentally friendly and energy efficient design.
Designing a reliable, efficient and sustainable building services system for this worldclass supertall building posed formidable challenges to all engineers. Using the same team who worked on the ICC in Hong Kong JRP worked to design and implement features that include the following engineering solutions:
A 55MVA transformer capacity is backed up by six 2MVA generators. A 4500kg cargo lift, backed up by four 10kV generators, transports power transformers to plantrooms at hundreds of metres above ground.
77 elevators, 45 of which are double decked passenger elevators, transport over 2000 people in five minutes, with travel from the ground floor to the 541m high Observation Deck minimised to around 60 seconds.
Double deck elevators trim down the core size and optimise the efficiency of building core to the maximum.
Strategic hydraulic zoning provides a cost effective design solution and system reliability for installation, operation flexibility and efficient maintenance.
The largest indoor cooling tower plant in southern China minimises pump power requirements
Use of CO2 sensors to optimise fresh air control , ice storage plant , high efficiency luminaries and regenerative power as energy efficiency and environmental friendly features.